As a materials engineer with expertise in mechanical testing and material simulation, I specialize in the design and development of tools tailored for conducting mechanical tests in environments prone to hydrogen exposure and/or stress corrosion. My work focuses on creating robust solutions that enable accurate and reliable assessments of material performance under challenging conditions.
About
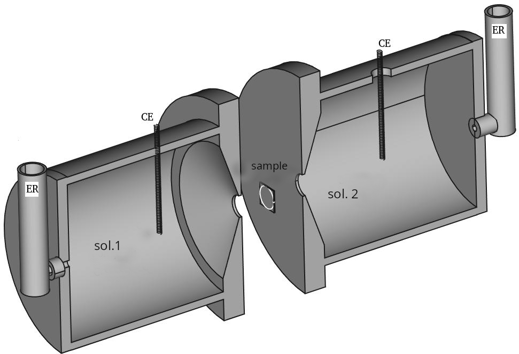
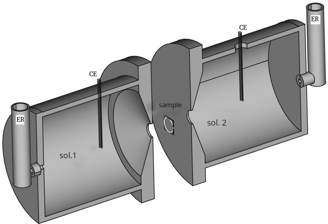
In the realm of materials engineering, the significance of electrochemical hydrogen permeation testing cannot be overstated. This testing method is pivotal in evaluating a material's resistance to hydrogen permeation, a critical consideration in applications ranging from hydrogen storage systems to pipelines. As an integral part of my portfolio, I take pride in having developed and designed an electrochemical hydrogen permeation cell, Figure 2. This specialized cell serves as a cutting-edge tool for precisely assessing a material's ability to avable the hydrogen permeation, providing valuable insights into its suitability for use in environments where hydrogen exposure is a concern. This accomplishment underscores my commitment to advancing materials engineering through innovative testing methodologies and bespoke design solutions.
Fig. 2: Permeation Cell Schematic - Public Domain Illustration
In my portfolio, I proudly showcase my project involving the design of a hydrogenation cell tailored for hydrogen embrittlement testing, particularly under sustained load and step-load conditions, Figure 1. This specialized cell is instrumental in assessing material properties in corrosive environments. The capability to perform hydrogenation under stress is crucial for a comprehensive understanding of a material's performance, ensuring its durability and integrity in real-world applications. The step-load testing further enhances the precision of evaluations, making this project a testament to my commitment to advancing materials engineering through innovative and impactful testing methodologies.
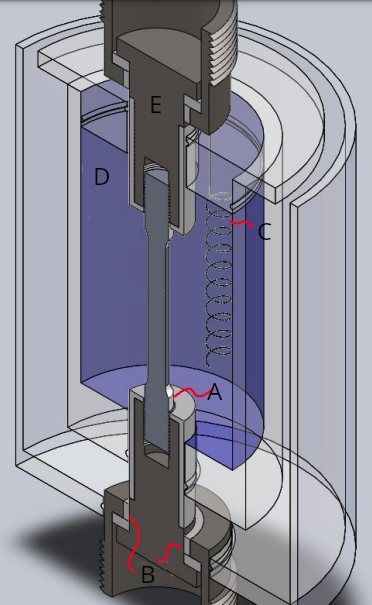
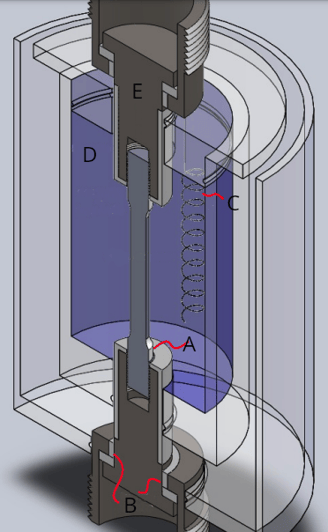
Mechanical Design Projects and Material Testing: A Portfolio Showcase
Fig. 1 Hydrogenation Cell Scheme for Specimen under Constant Stress. Public Domain Illustration Included in My Thesis
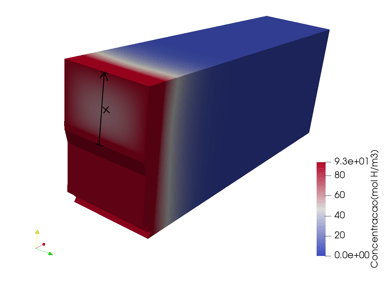
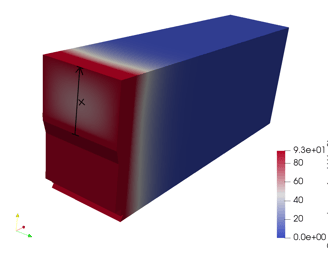
Hydrogenation in complex samples
I proudly showcase my contribution to the field of materials testing through the development of a mechanical testing tool. This specialized tool was designed for measuring crack propagation using CTOD (Crack Tip Opening Displacement) in samples pre-exposed to hydrogen. The innovative approach involves assessing hydrogen-induced cracking, a critical concern in material integrity.
The accompanying figure illustrates hydrogen concentration profiles for various durations, calculated using finite element methods. This tool not only enables precise measurement of crack propagation but also provides a deeper understanding of how hydrogen influences the fracture behavior of materials. This project underscores my commitment to advancing materials engineering, combining mechanical testing and numerical simulations to address challenges in hydrogen-related material degradation.
In my portfolio, I feature expertise in the comprehensive analysis of mechanical stresses, hydrostatics, plastic deformation, and the calculation of hydrogen concentration profiles in notched circular samples, Figure 4. Leveraging solid mechanics and mass transport models, I have successfully employed advanced methodologies to evaluate the intricate interplay of these factors. This work demonstrates my proficiency in utilizing a multidisciplinary approach to assess material behavior, particularly in scenarios involving circular notches, providing valuable insights for applications in hydrogen-induced cracking and related phenomena.
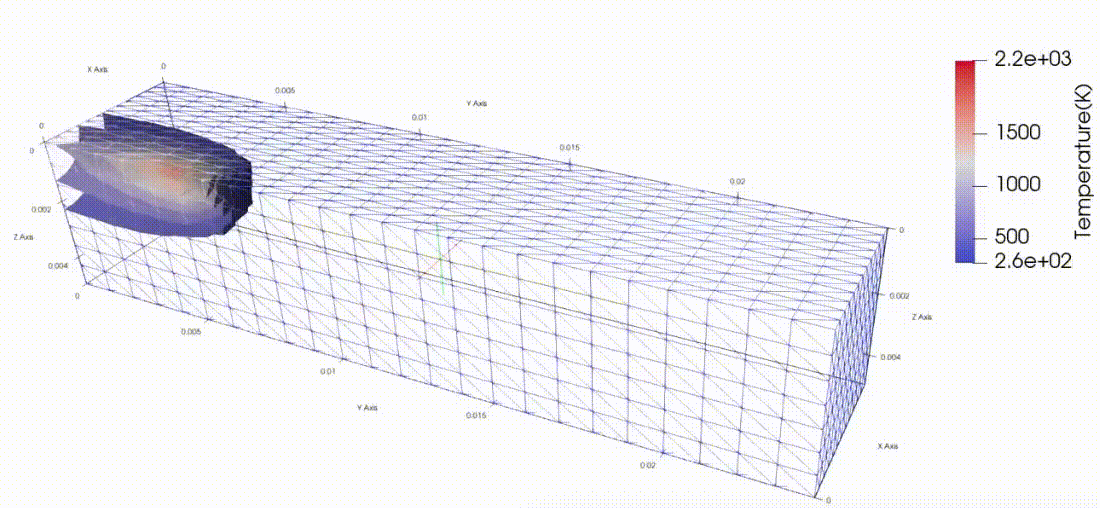
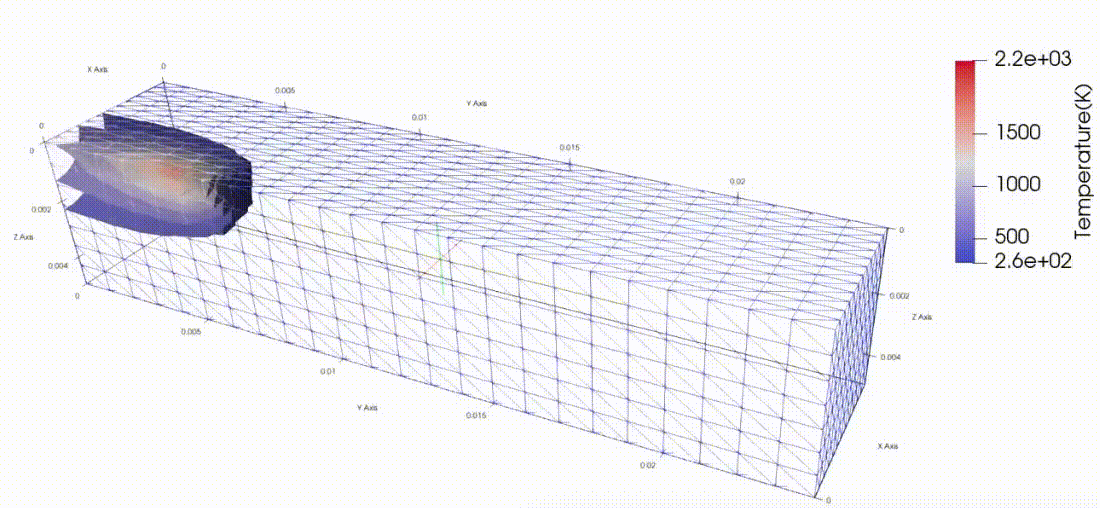
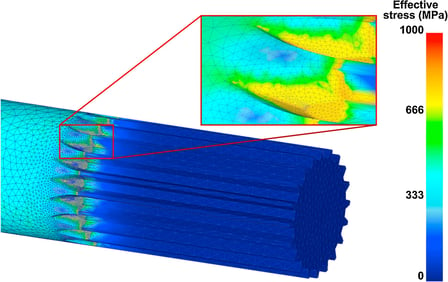
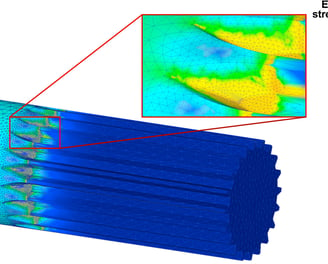
Heat Input Optimization in Welding: Special Steels and Superalloys.
In my portfolio, I feature a noteworthy project centered on the design and simulation of heat input in welding processes involving special steels and superalloys like Inconel. This endeavor holds paramount importance in understanding and optimizing the thermal aspects of welding, contributing to enhanced material properties and structural integrity.
The project incorporates finite element-derived welding thermal curves and analytical solutions for heat transport equations, allowing for a detailed analysis of the welding process. Leveraging these tools, I can accurately estimate the size of the heat-affected zone and comprehend thermal curves between welding passes. This capability not only enables precise estimations but also facilitates the calibration of mathematical welding models. Such insights are instrumental in fine-tuning welding parameters and optimizing the overall welding process for alloys with stringent performance requirements, reinforcing my commitment to excellence in materials engineering.
Simulation of weld joint Inconel 718. Temperature is estimated by finite element method. Laplace equations with double ellipsoid source function. Python and open-source library, Figure 6.
In this analysis, I played a key role in investigating the premature failure of a racing car's half-shaft after approximately 100 km of use, Figure 5. Through metallographic, chemical, and mechanical analyses, along with fractography and finite element analysis, I identified that the alloy steel used did not meet specifications, resulting in lower strength and insufficient fatigue resistance. The fracture was a combination of torsional fatigue crack propagation and overload ductile fracture in the spline section of the half-shaft. This experience showcases my expertise in failure analysis and finite element techniques for resolving structural issues.
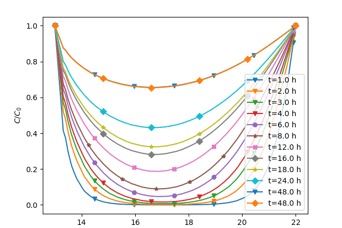
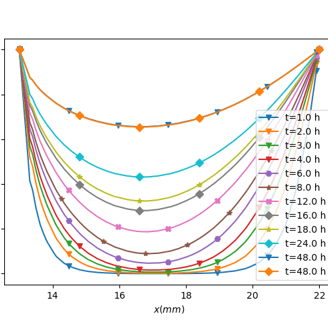
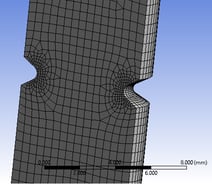
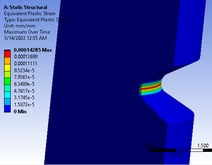
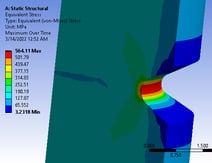
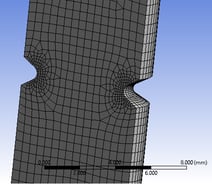
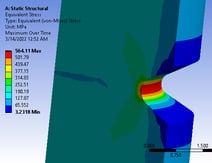
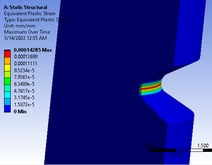
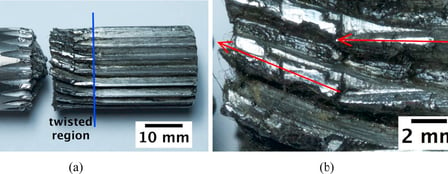
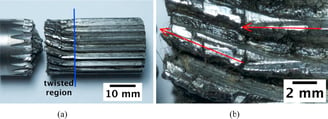
Macroscale simulation
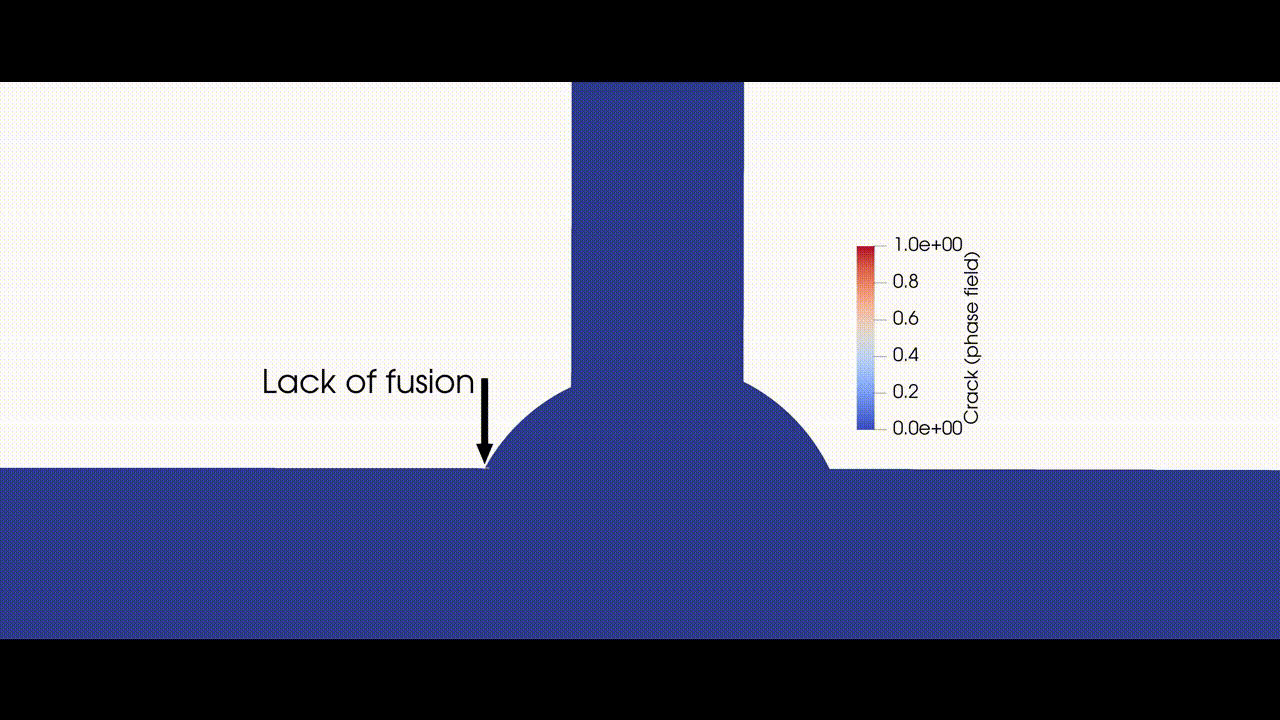
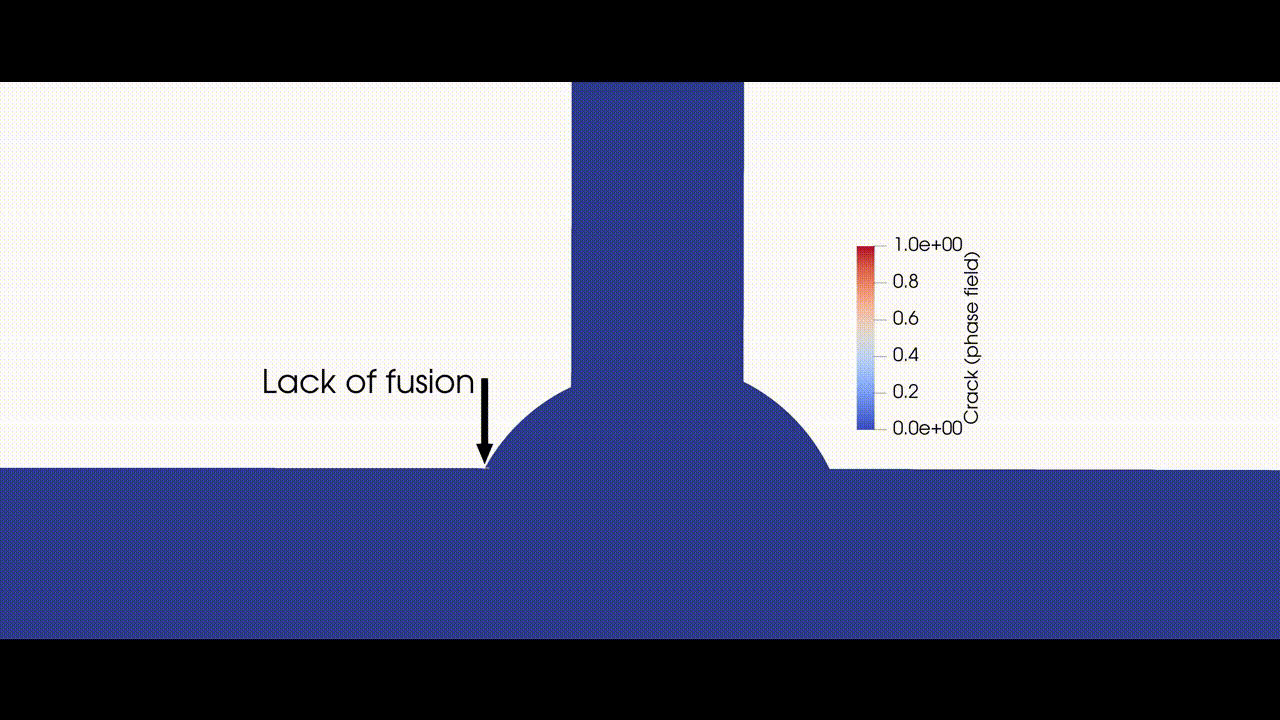
Failure analysis
I highlight my proficiency in conducting fracture process analyses using phase field modeling through finite element simulations, particularly at the macro scale and in complex geometries, Figure 7. I specialize in scenarios involving intricate structures like welded joints with defects, cracks, or lack of fusion. Depending on the problem or loading conditions, the defect may initiate crack propagation in a welded joint or at another stress concentration point. The figure presented illustrates that even in the presence of a lack of fusion, the fracture may or may not initiate from the defect, depending on the loading type. My ability to navigate and model these complex fracture scenarios demonstrates my expertise in utilizing finite element analysis for robust and insightful mechanical engineering assessments.
Fig 3. Hydrogen Concentration Calculation Simulation for Notched Specimen (a)simulation, (b) Concentration Profile: An Example
(a)
(b)
Fig. 4 Hydrogen Concentration Calculation Simulation for Notched Specimen (a)mesh, (b) stress and (c) displacement
Fig. 6: Temperature Profile Generated by Welding Heat Source on Sheet Metal.
Fig. 5 Premature Failure of Racing Car's Half-Shaft: (a) Component, (b) Fracture Detail, (c) Simulation
Fig. 7. Simulation of welded joint with lack of fusion and collapse prediction in various scenarios.
(c)
Macro mechanical analyses and hydrogen
Microscale simulation
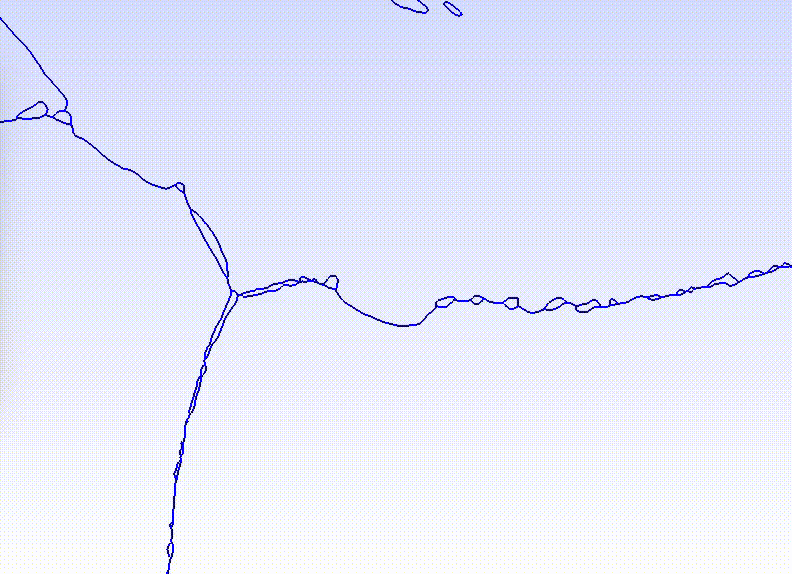
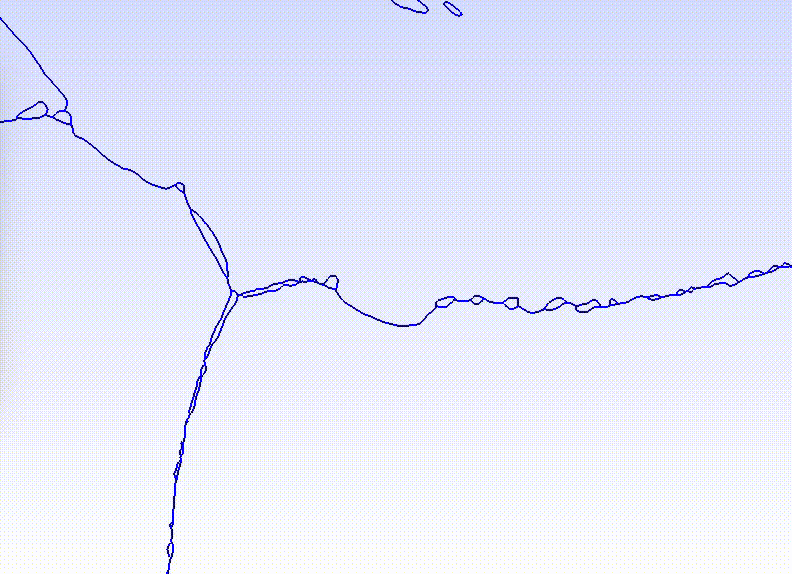
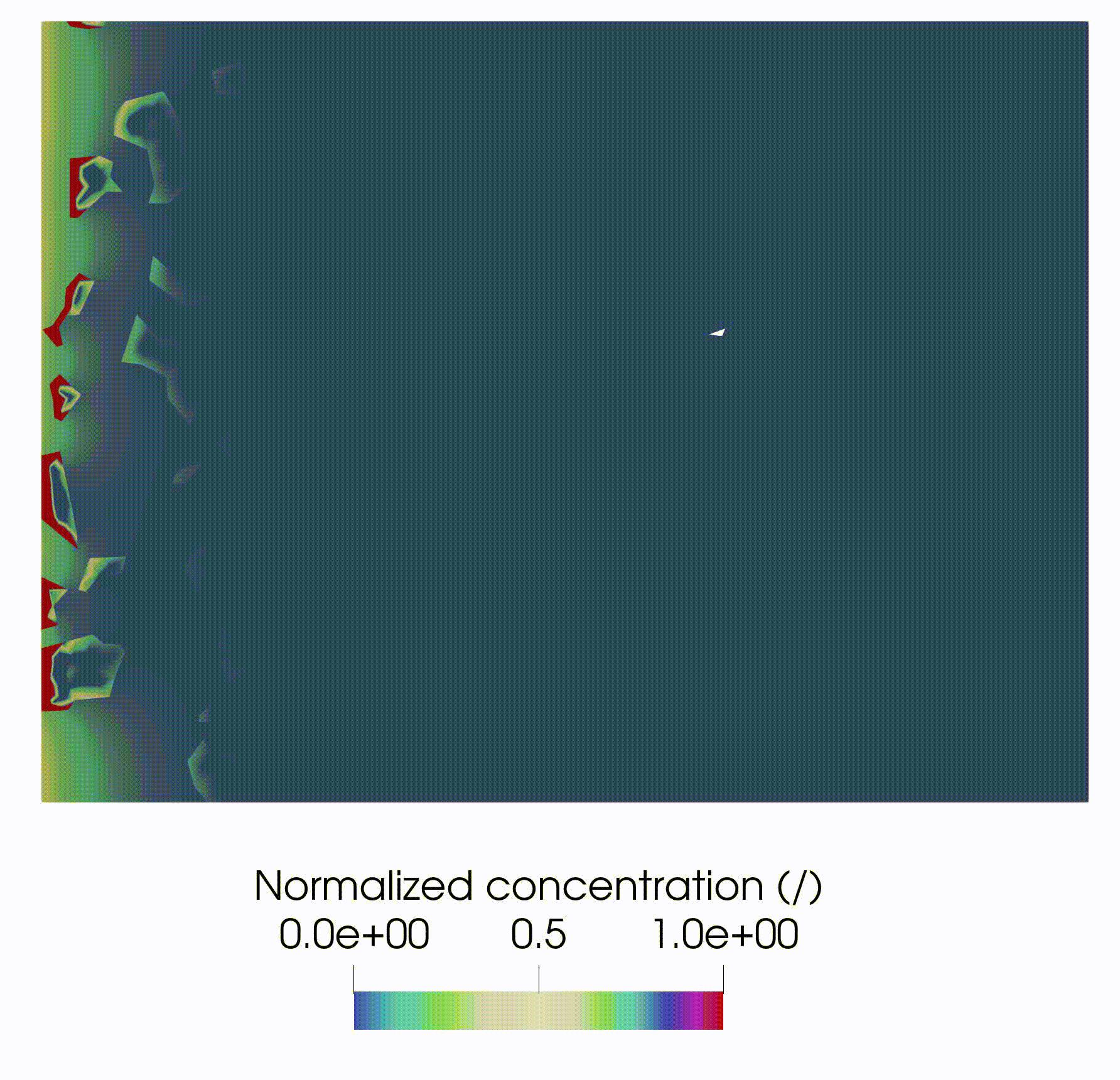
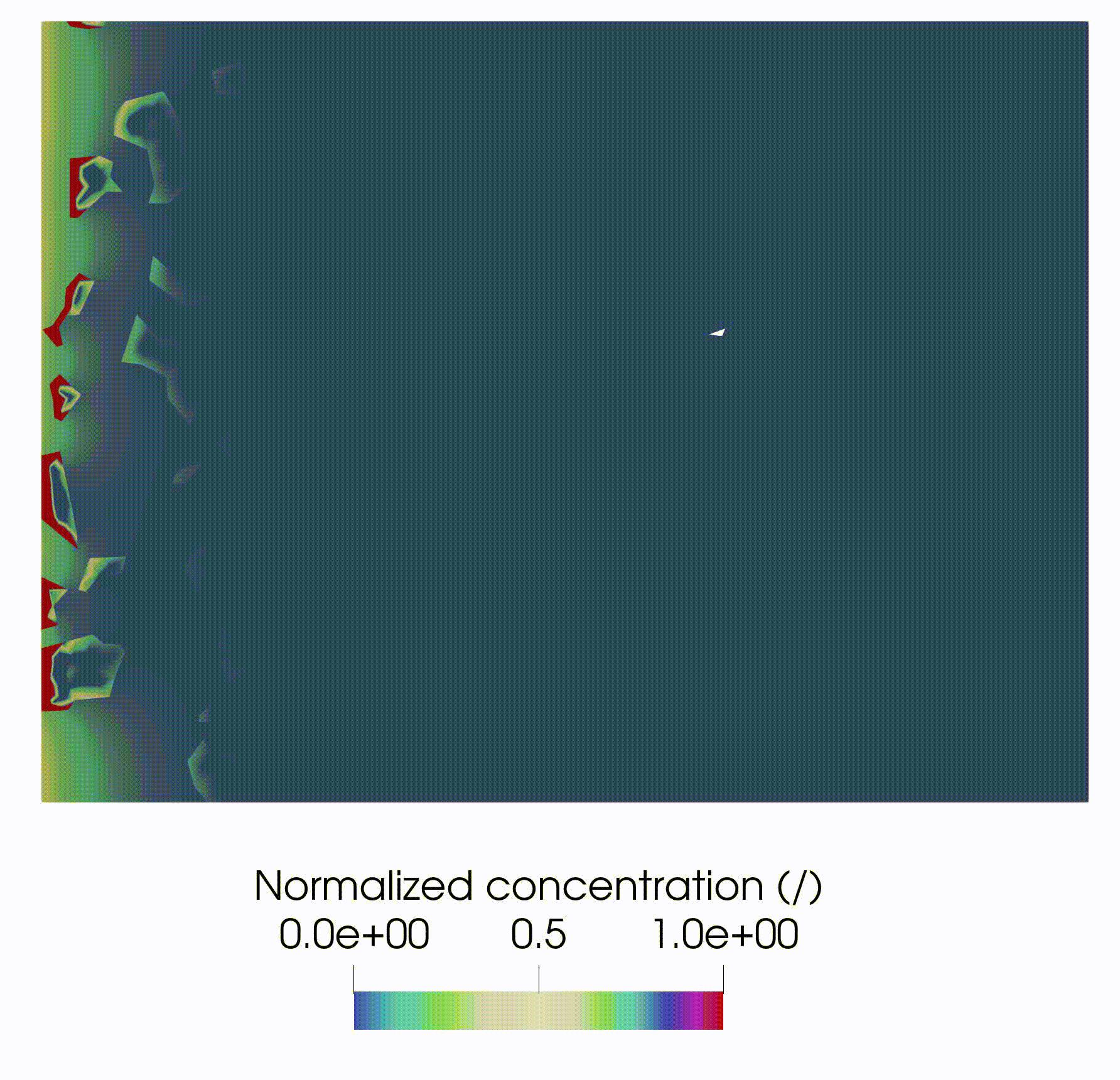
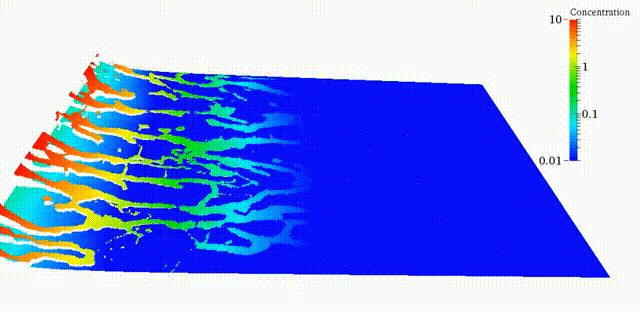
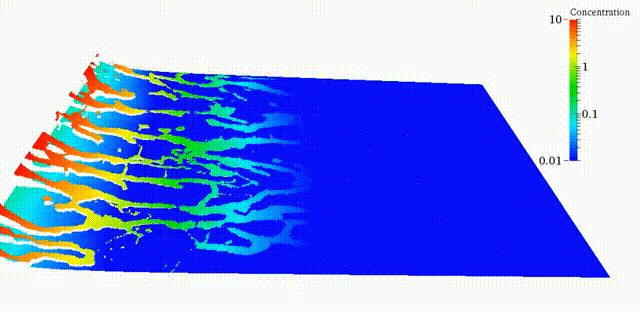
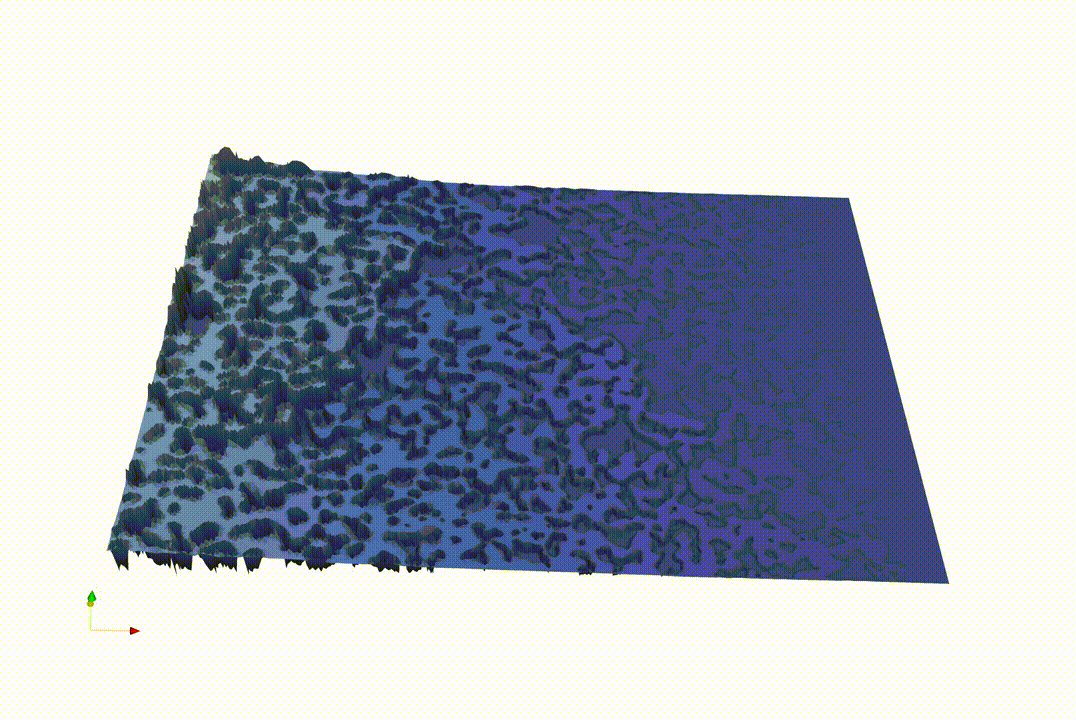
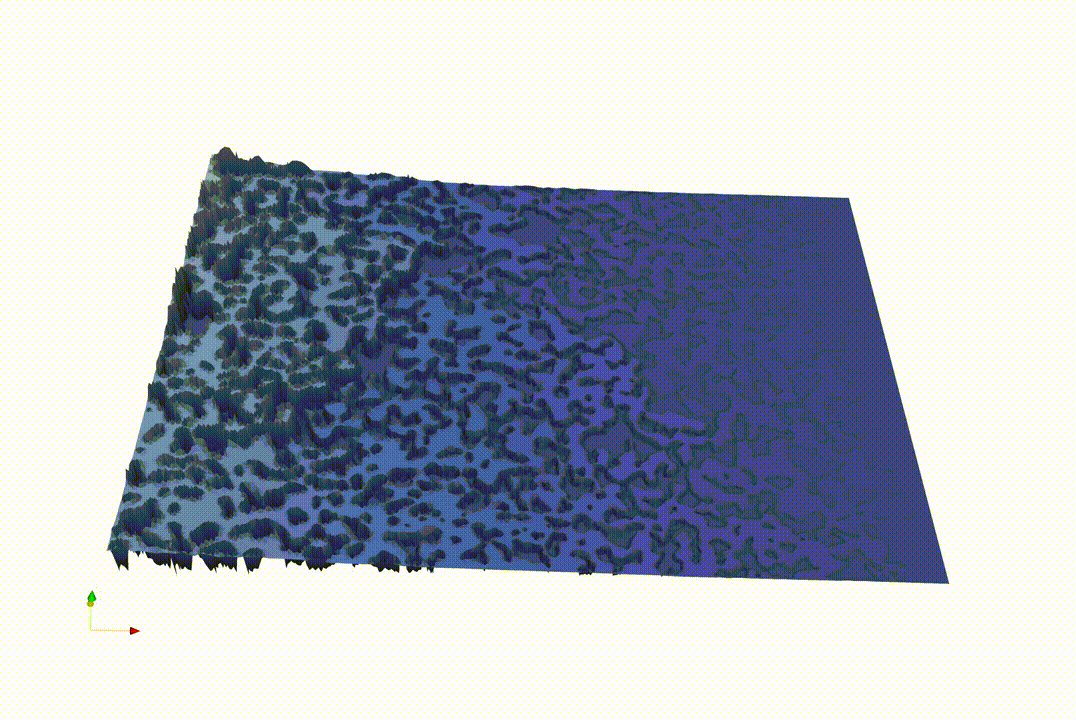
Explore my portfolio to witness my proficiency in generating meshes from microscopy images. This intricate process involves meticulous pre-processing and subsequent vectorization, where phases and contours are transformed into adaptable meshes. I employ auditable open-source programs and libraries, allowing for transparency and reliability throughout the process. The mesh type and interpolation degree are customizable, catering to the unique demands of each problem. Refinement is strategically implemented, focusing on the region under analysis and the necessary characteristics for problem convergence.
Displayed in the accompanying Figure 8 is a mesh generated from a complex multiphase microstructure, showcasing grain boundaries between different phases and precipitates at phase interfaces and within grain interiors. This process exemplifies my dedication to precision and adaptability, essential for addressing diverse engineering challenges.
Mesh generation on microescale
Computational modelling, multiphysics simulation
Fig. 10. Simulation of Vein-Like Microstructure.
Within my portfolio, I showcase my adeptness in producing simulations of diffusive processes within complex multiphase microstructures. From microstructures featuring isolated islands(Figure 9), vein-like patterns(Figure 10), my expertise extends to various intricate configurations . I specialize in simulating diffusive phenomena in these microenvironments, capturing the nuanced behavior of materials inclued interfacial problems, Figure 11.
Moreover, my skill set includes the analysis of interfaces between materials exhibiting distinct physical properties. This involves a comprehensive understanding of how different materials interact within the microstructure, allowing for precise predictions and insights. The ability to simulate diffusive processes in multifaceted microstructures, coupled with proficiency in interface analysis, exemplifies my commitment to providing in-depth and versatile solutions in the realm of materials engineering.